In-Situ Measurement to Measuring Process Conditions at High Speed.
Tunable diode laser spectrometers (TDLS) allow for real-time gas analysis to increase efficiency, safety, throughput, quality, and environmental compliance. The non-contacting sensor allows measurement under severe conditions, such as high temperature, high pressure, corrosive/abrasive conditions, high dust concentration, etc. Maintenance can also be performed without taking the process offline because the TDLS is isolated from the process. The TDLS is a robust process analyzer that contributes to stable and efficient operation.
>>> Application Notes
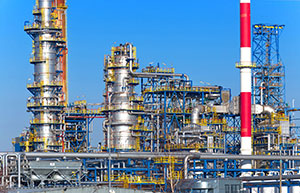
- In-situ measurement in harsh environments
- Measurement up to 1500℃
- Up to 30m optical path lengths
- Optimal for SIS integration via SIL 2 and 3 certification
Maximize uptime in aggressive processes
Various plant units and piping may contain pressurized, high-temperature, corrosive, combustible, and/or toxic gases which may be problematic for traditional technologies. The TDLS8000 can detect the concentration of process gas in real time without direct contact to allow for quick response to optimize process availability without sacrificing measurement availability.
>>> Principles
Improved OPEX and safety
The TDLS8000 helps reduce total OPEX and maximize output safely
Example: The TDLS8000 can measure up to 30m over the entire length of a furnace at the top of the radiant section to analyze for efficient combustion. Based on gas concentrations, operators can optimize the air-fuel ratio and analyze heat transfer efficiency while ensuring a safe environment.
>>> Solutions
>> Yokogawa TDLS technology can help to improve operational safety and emissions in a variety of industries <<
The TDLS8000 was designed to help users meet a variety of operational standards and is capable of being integrated into SIL2 and SIL3 applications.
>>> Operational Improvement
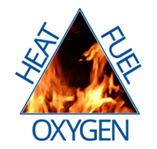
-
In-Situ Gas Analyzer TDLS8000
Yokogawa’s new TDLS™8000 houses all of the industry’s leading features in one robust device. The platform design is for in situ measurements which negate the need for sample extraction and conditioning.
-
Probe type Tunable Diode Laser Spectrometer TDLS8200
Sampling unnecessary, installation flange is only on one side, installation cost is reduced by half while keeping high speed measurement / high speed response. It can be easily exchanged from existing equipment.
-
High Sensitivity Laser Spectrometer TDLS5500
TDLS5500 is a computerized device that measures the amount of gas contained in the process in real time.
Details
TDLS contributes to improving your work.
Features of TDLS Series
- Measurement of oxygen, carbon monoxide, methane, ammonia, moisture, carbon dioxide, and other gases in seconds
- No sampling equipment is required for the majority of measurements, eliminating a large portion of maintenance
- The only process TDLS platform capable of measuring up to 30m
- Measurements can be made in high temperature, high pressure, corrosive/abrasive, and high dust conditions because the sensor does not come in contact with process gas
- Ideal for critical applications with a SIL-rated fast speed of response
- Maximize efficiency, consider the environment, and reduce emissions of CO, NOx, etc.
Settling with legacy technologies
In a world which is continuously evolving in the direction of increased process optimization while maintaining safe operating state, it’s difficult to retain a competitive advantage without adopting new measurement techniques to stay cutting-edge.
>>> Principles
TDLS provides a safe, efficient and cost-effective solution.
Basic Concept and Measurements of Laser Gas analyzer
Measurement principle of a laser gas analyzer
The tunable diode laser absorption spectrometers (TDLAS) operate by measuring the amount of a laser light that is absorbed as it travels through the gas being measured. Because the sensor does not have contact with the process and there are no moving parts, maintenance is minimized, which decreases downtime and reduces the long-term cost of ownership (LTCO).
The attenuation due to IR absorption is determined by Lambert Beers'Law.
Lambert Beers'Law
Absorption of IR-Radiation
A highly reliable measurement in varying steam conditions is possible due to Yokogawa’s unique spectral analysis methodology
Yokogawa Electric's original spectral area method is hardly affected by interferences of other gases, and it can be measured with high accuracy by temperature and pressure-compensation.
An integral reference cell retains measurement integrity, even in low absorption streams
The use of a reference cell keeps the peak position locked during trace measurement when the absorption signal is weak.
Up to 50 days of historical data, spectra, and all setting changes are accessible
This data is useful for remote troubleshooting of process issues long after upsets have occurred.
Increased measurement capabilities have allowed our users to safely increase operating efficiencies while reducing emissions.
- In situ analysis
Improves safety and process controlling capability due to near real time response - Tunable laser
No moving part so that no consumable exists - Non-contact sensor
Operates in a harsh environment and minimizes maintenance - Long-pass optical sensor
Represents the entire process measured whereas inserted or extractive measurement reflects only a spot.
The TruePeak Tunable Diode Laser Spectrometers operate by measuring the amount of a laser light that is absorbed as it travels through the gas being measured. Involving no sensor contact with the process and no moving parts, it leads to a high mean time between failures (MTBF) and hence a low long term cost of ownership (LTCO).
Fired heaters are integral to industrial processes, including hydrocarbon processing and power generation. Specifically designed for the reaction of fuel and air to produce extremely high gas temperatures, heaters transfer this energy to potentially highly flammable process fluids via heat exchangers. They consume large quantities of fuel, produce large quantities of emissions and are a potential safety hazard to personnel and plant.
Yokogawa TDLS analyzers help control fired heater combustion with ever greater accuracy and reliability. There are measurable rewards for operating fired heaters at Low Excess Air (LEA) levels. In LEA combustion control, the lowest level of fuel is consumed and the products of combustion are cooled the least by unused excess air.
The cost benefits of these efficiencies are considerable, with just a single percentage saving in fuel enabling savings of tens or even hundreds of thousands of dollars per year. Controlling air levels just above the point at which incomplete combustion starts also enables the "cleanest burn," helping plants meet environmental emissions requirements. This in particular reduces the emission of NOx.
Combustion
Maintaining operational efficiency in your furnaces to maximize throughput and minimize fuel consumption while ensuring safe operation is truly a difficult challenge.
Conventional analyzer technologies, such as zirconia and catalytic bead measurements, are point style measurements which can fail to completely capture what is happening in your furnace. In addition to being a potential ignition source, zirconia can have its reading lowered in the presence of combustibles. COE analysis has its own issues due to the minutes-long response time required for typical breakthrough levels in the thousands of ppm in the radiant section of a fired asset, and often require a separate sensor for CH4 measurement. Such issues can have a large impact on how safely your furnace is being operated.
The modern unit operator needs access to the most trustworthy data available to quickly mitigate the occurrence of an unsafe condition if they’re going to optimize asset performance.
The introduction of Yokogawa’s Tunable Diode Laser Spectrometer (TDLS) technology allows for the real-time, in-situ, interference free, reliable, and accurate measurement of oxygen and CO to maximize efficiencies.
It’s a major advance in supporting the entire facility in operating the asset safely and efficiently.
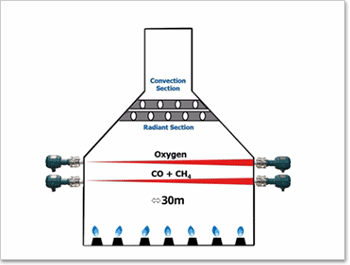
Features and advantages of Yokogawa's TDLS technologies
- Real-time data for control
The efficiency is maximized because and safely improves operation efficiency as well as emissions because the air/fuel ratio is always optimized - Laser analysis
The new technology enables the adoption of industry best practices. - Non-contact sensor
Operates in a harsh environment and minimizes maintenance - Long-path optical sensor
Long path average measurement eliminates hot spots hence enables long lifetime of the heat exchange pipe (minimization of costs).
Safety / Process
When it comes to understanding what is happening in your furnace, a reliance on limited data outputs from conventional analyzer technology places a greater onus on the skills of the operator.
TDLS technology reduces the burden on operator competence and the potential for human error by delivering the most trustworthy data on the entire furnace as quickly as possible for optimal asset efficiency and safety.
It’s imperative you have the ability to detect, measure and control LOC (Limiting Oxygen Concentration) to ensure the safety of your facility and your workmates.
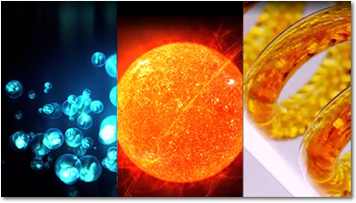
Our customers' operating safety and operating efficiencies have enabled us to reduce operating costs and reduce CO2 and NOx emissions.
Resources
Storage tanks are used in a variety of industries ranging from holding crude oil to holding feedstock for vinyl chloride monomer (VCM).
In maintaining and managing industrial plants, monitoring waste water pH/ORP is both a legal obligation and an unavoidable necessity for protecting the environment. Monitoring without an attentive eye can lead to severe consequences.
Considering safety and environmental issues such as combustion efficiency and decreasing NOX and CO in exhaust gas, it has become important to control O2 concentration in garbage incineration processes.
In recent years, shale gas extraction technology has made rapid progress, inducing a shale gas revolution mainly in the USA. Thus, the need for analysis of hydrocarbon gases, including natural gas, is expected to grow rapidly. Traditionally gas chromatography has been used for the analysis of hydrocarbon gases; it can accurately measure the concentration of each hydrocarbon component in a sample of natural gas.
Spectrometric technology can assess many critical characteristics about products, but it has limits. It can be challenging to determine when the line has been crossed
With fired heaters, users hope to get greater efficiency and reduced emissions but often are disappointed. Given the number of fired heaters operating every day and their importance in the process industries, any improvements realized across the board will have huge impacts. More units can reach their potential with some simple changes in work practices and technology upgrades.
The EPA rule, 40 CFR 63 Subparts CC and UUU, is forcing refineries to monitor flares. Fortunately, modern analyzer technology makes it possible to meet the requirements, generate the necessary reports, and stay in compliance.
Here’s how to select the right analyzer to meet these demands.
Downloads
Instruction Manuals
General Specifications
Technical Information
Drawings
- IF8000 Isolation Flange for TDLS8000 (151 KB)
News
-
Press Release Apr 6, 2021 Yokogawa Adds TDLS8200 Probe Type Tunable Diode Laser Spectrometer to Its OpreX Analyzer Lineup
- Simultaneous measurement of oxygen, carbon monoxide, and methane concentrations for optimum combustion control in heating furnaces -
Looking for more information on our people, technology and solutions?
Contact Us